Nissan Maxima Service and Repair Manual: Fuel tank
Exploded View
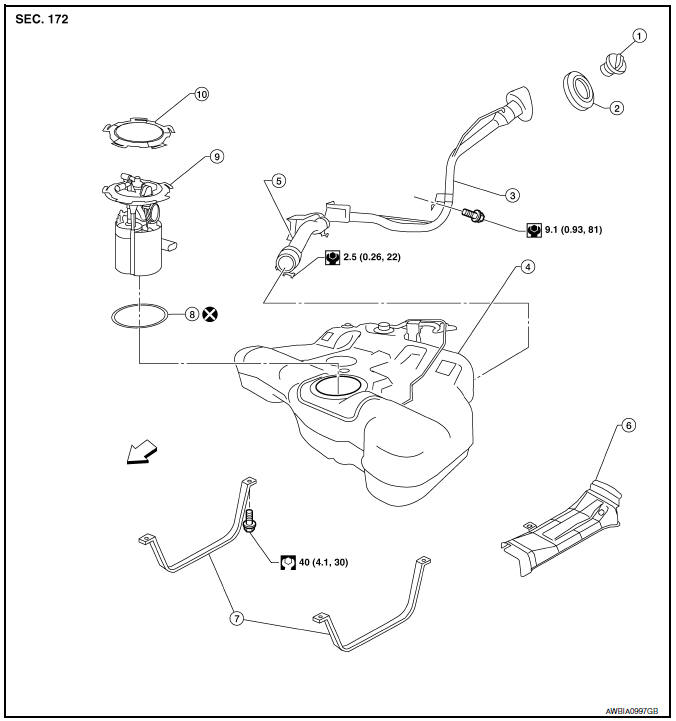
- Fuel filler cap
- Grommet
- Fuel filler tube
- Fuel tank
- Fuel filler hose
- Fuel tank protector
- Fuel tank mounting straps
- O-ring
- Fuel level sensor, fuel filter and fuel pump assembly
- Lock ring
Front
Removal and Installation
WARNING: Read "General Precautions" before working on
the fuel system. Refer to GI-27, "General Precautions".
NOTE:
When removing components such as hoses, tubes/lines, etc., cap or plug openings
to prevent fluid from spilling.
REMOVAL
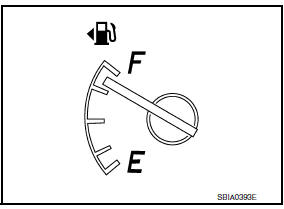
- Disconnect the battery negative terminal. Refer to PG-67, "Removal
and Installation (Battery)".
- . Open the fuel filler cap to release the pressure inside the fuel tank.
- Release fuel pressure from fuel line. Refer to EC-592,
"Inspection".
- Check the fuel level with the vehicle on a level surface. If the
fuel gauge indicates more than the level as shown (7/8 full), drain
the fuel from the fuel tank until the fuel gauge indicates a level at or
below as shown (7/8 full).
- In case the fuel pump does not operate, use the following
procedure.
- Insert fuel tubing of less than 25mm (0.98in) diameter into the
fuel filler tube through the fuel filler opening to drain fuel from the
fuel filler tube.
- Disconnect the fuel filler hose from the fuel filler tube.
- Insert fuel tubing into the fuel tank through the fuel filler hose
to drain fuel from the fuel tank.
- As a guide, the fuel level reaches or is less than the level on
the fuel gauge as shown, when approximately 10
(2 5/8 US gal, 2 1/4 Imp gal) of fuel is
drained from a full fuel tank.
- Remove the rear seat cushion. Refer to SE-70, "Removal and Installation"
(with fixed seatback, WITH CLIMATE CONTROLLED SEATS), SE-73, "Removal and
Installation" (with split seatback, WITH CLIMATE CONTROLLED SEATS),
SE-128, "Removal and Installation" (with fixed seatback, W/O CLIMATE
CONTROLLED SEATS) SE-131, "Removal and Installation" (with split seatback,
W/O CLIMATE CONTROLLED SEATS).
- Turn the four retainers 90 degrees in a clockwise direction and
remove the fuel pump inspection hole cover.
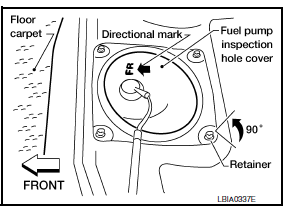
- Disconnect the fuel level sensor, fuel filter, and fuel pump assembly
harness connector, EVAP hose quick connector, and fuel feed hose quick
connector
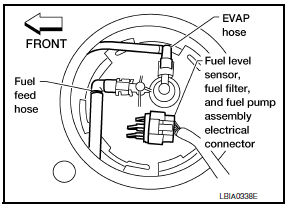
- Disconnect the quick connectors as follows:
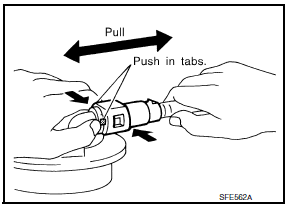
- Hold the sides of the connector, push in tabs and pull out the
tube.
- If the connector and the tube are stuck together, push and pull
several times until they start to move. Then disconnect them by pulling.
CAUTION:
- The tube can be removed when the tabs are completely
depressed. Do not twist it more than necessary.
- Do not use any tools to remove the quick connector.
- Keep the resin tube away from heat. Be especially careful
when welding near the tube.
- Prevent acid liquid such as battery electrolyte, from getting
on the resin tube.
- Do not bend or twist the tube during installation and removal.
- Only when the tube is replaced, remove the remaining retainer
on the tube or fuel level sensor, fuel filter, and fuel pump assembly.
- When the tube or fuel level sensor, fuel filter, and fuel pump
assembly is replaced, also replace the retainer with a new one (green
colored retainer).
- To keep the connecting portion clean and to avoid damage
and foreign materials, cover them completely with plastic bags or
something similar.
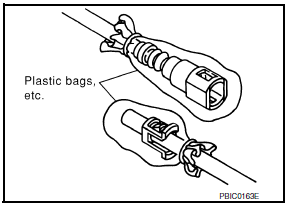
- Remove the center exhaust tube, with muffler. Refer to EX-5, "Removal
and Installation".
- Disconnect the fuel filler hose and recirculation hose at the fuel
tank side.
- Disconnect the three parking brake cable mounting brackets on each cable
and position the cables out of the way. Refer to PB-6, "Exploded View".
- Remove rear stabilizer bar clamps, then allow stabilizer bar to
hang. Refer to RSU-13, "Removal and Installation".
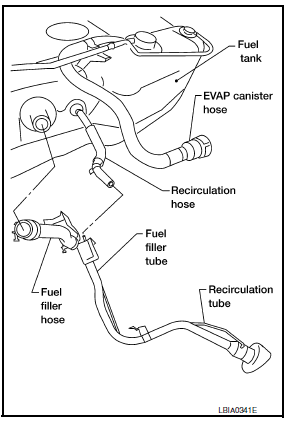
- Remove EVAP canister bolts. Then without disconnecting hoses, position
EVAP canister aside. Refer to FL-14, "Removal and Installation (EVAP
Canister)".
- Remove the fuel tank protector.
- Remove the fuel tank mounting strap bolts and mounting straps
while supporting the fuel tank with a suitable jack.
- Remove the fuel tank.
- If replacing the fuel tank, remove the fuel level sensor unit,
fuel filter and fuel pump assembly to transfer to the new fuel tank.
Remove and discard the O-ring.
CAUTION: Do not reuse O-ring.
INSTALLATION
Install in the reverse order of removal paying attention to the following.
CAUTION: Do not reuse O-ring.
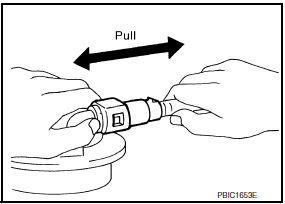
- Check the connection for damage or any foreign materials.
- Align the connector with the tube, then insert the connector
straight into the tube until a click is heard.
- After the tube is connected, make sure the connection is secure by
performing the following checks:
- Pull on the tube and the connector to make sure they are securely
connected.
- Visually confirm that the two retainer tabs are connected to the
quick connector.
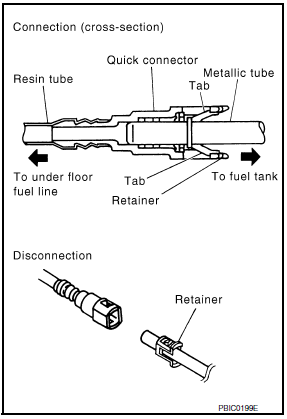
INSPECTION AFTER INSTALLATION
Use the following procedure to check for fuel leaks.
- . Turn the ignition switch ON (without starting the engine). Then check
the connections for fuel leaks by applying fuel pressure to the fuel
piping.
- Run the engine and check for fuel leaks at the fuel system tube
and hose connections.
FUEL LEVEL SENSOR UNIT, FUEL FILTER AND FUEL PUMP ASSEMBLY
Exploded View
Lock ring
Fuel level sensor, fuel filter and fuel pump assembly
O-ring
Fuel tank Front
Removal a ...
Removal and Installation (EVAP Canister)
EVAP control system pressure sensor
EVAP canister
O-ring
EVAP canister vent control valve
O-ring
NOTE: The EVAP canister vent contr ...
Other materials:
Front disc brake
Disassembly and Assembly
Union bolt
Copper sealing washer
Brake hose
Cap
Bleed valve
Sliding pin bolt
Piston seal
Piston
Piston boot
Cylinder body
Upper sliding pin
Lower sliding pin bolt
Torque member bolt
Washer
Sliding pin boot
Bushing
Torque memb ...
B2128 UART communication line
Description
Driver seat control unit performs UART communication with the automatic drive
positioner control unit using 1 communication line. Driver seat control unit
receives the operation signals of ADP steering switch, door mirror remote
control switch and the position signals of tilt sens ...
VDC off indicator lamp
Description
Component Function Check
1.VDC OFF INDICATOR LAMP OPERATION CHECK 1
Check that the lamp illuminates for approximately 2 seconds after the
ignition switch is turned ON.
2.VDC OFF INDICATOR LAMP OPERATION CHECK 2
Check that the VDC OFF indicator lamp in the combination meter tur ...