Nissan Maxima Service and Repair Manual: P0420, P0430 three way catalyst function
DTC Logic
DTC DETECTION LOGIC

The ECM monitors the switching frequency ratio of air fuel ratio (A/F)
sensor 1 and heated oxygen sensor 2.
A three way catalyst (manifold) with high oxygen storage capacity
will indicate a low switching frequency of heated oxygen sensor 2.
As oxygen storage capacity decreases, the heated oxygen sensor 2
switching frequency will increase.
When the frequency ratio of A/F sensor 1 and heated oxygen sensor
2 approaches a specified limit value, the three way catalyst (manifold)
malfunction is diagnosed.

DTC CONFIRMATION PROCEDURE
1.INSPECTION START
2.PRECONDITIONING
If DTC Confirmation Procedure has been previously conducted, always perform
the following before conducting
the next test.
- Turn ignition switch OFF and wait at least 10 seconds.
- Turn ignition switch ON.
- Turn ignition switch OFF and wait at least 10 seconds.
TESTING CONDITION:
Do not maintain engine speed for more than the specified minutes below.
3.PERFORM DTC CONFIRMATION PROCEDURE-I
With CONSULT
- Turn ignition switch ON and select "DATA MONITOR" mode with CONSULT.
- Start engine and warm it up to the normal operating temperature.
- Turn ignition switch OFF and wait at least 10 seconds.
- Turn ignition switch ON.
- Turn ignition switch OFF and wait at least 10 seconds.
- Start engine and keep the engine speed between 3,500 and 4,000 rpm
for at least 1 minute under no load.
- Let engine idle for 1 minute.
- Check that "COOLAN TEMP/S" indicates more than 70C (158F).
If not, warm up engine and go to next step when "COOLAN TEMP/S" indication
reaches to 70C (158F).
- Open engine hood.
- Select "DTC & SRT CONFIRMATION" then "SRT WORK SUPPORT" mode with
CONSULT.
- Rev engine between 2,000 and 3,000 rpm and hold it for 3 consecutive
minutes then release the accelerator
pedal completely.
- Check the indication of "CATALYST".
4.PERFORM DTC CONFIRMATION PROCEDURE-II
- Wait 5 seconds at idle.
- Rev engine between 2,000 and 3,000 rpm and maintain it until
"INCMP" of "CATALYST" changes to
"CMPLT" (It will take approximately 5 minutes).
5.PERFORM DTC CONFIRMATION PROCEDURE AGAIN
- Stop engine and cool it down to less than 70C (158F).
- Perform DTC CONFIRMATION PROCEDURE again.
6.PERFORM DTC CONFIRMATION PROCEDURE-III
Check 1st trip DTC
7.PERFORM COMPONENT FUNCTION CHECK
Perform component function check
NOTE:
Use component function check to check the overall function of the three way
catalyst (manifold). During this
check, a 1st trip DTC might not be confirmed.
Component Function Check
1.PERFORM COMPONENT FUNCTION CHECK
Without CONSULT
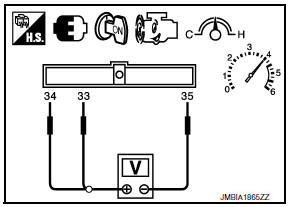
- Start engine and warm it up to the normal operating temperature.
- Turn ignition switch OFF and wait at least 10 seconds.
- Turn ignition switch ON.
- Turn ignition switch OFF and wait at least 10 seconds.
- Start engine and keep the engine speed between 3,500 and 4,000 rpm
for at least 1 minute under no load.
- Let engine idle for 1 minute.
- Open engine hood.
- Check the voltage between ECM harness connector terminals
under the following conditions.

Diagnosis Procedure
1.CHECK EXHAUST SYSTEM
Visually check exhaust tubes and muffler for dents.
2.CHECK EXHAUST GAS LEAKAGE
- Start engine and run it at idle.
- Listen for an exhaust gas leakage before the three way catalyst
(manifold).
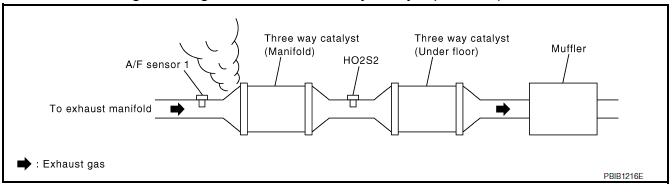
3.CHECK INTAKE AIR LEAKAGE
Listen for an intake air leakage after the mass air flow sensor.
4.CHECK IGNITION TIMING
Check idle speed and ignition timing.
5.CHECK FUEL INJECTORS
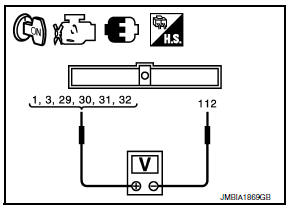
- Stop engine and then turn ignition switch ON.
- Check the voltage between ECM harness connectors.
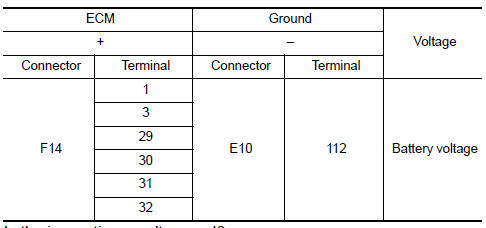
6.CHECK FUNCTION OF IGNITION COIL-I
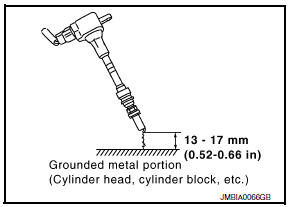
CAUTION:
Perform the following procedure in a place with no combustible objects and good
ventilation.
- Turn ignition switch OFF.
- Remove fuel pump fuse in IPDM E/R to release fuel pressure.
NOTE:
Do not use CONSULT to release fuel pressure, or fuel pressure applies again
during the following procedure.
- Start engine.
- After engine stalls, crank it two or three times to release all
fuel pressure.
- Turn ignition switch OFF.
- Remove all ignition coil harness connectors to avoid the
electrical discharge from the ignition coils. Refer
to EM-42, "Removal and Installation (LH)" or EM-42, "Removal and Installatio
(RH)".
- Remove ignition coil and spark plug of the cylinder to be checked.
- Crank engine for 5 seconds or more to remove combustion gas in the
cylinder.
- Connect spark plug and harness connector to ignition coil.
- . Fix ignition coil using a rope etc. with gap of 13 - 17 mm (0.52 -
0.66 in) between the edge of the spark plug and grounded metal
portion as shown in the figure.
- Crank engine for about 3 seconds, and check whether spark is
generated between the spark plug and the grounded metal portion.
Spark should be generated
CAUTION:
- Never place the spark plug and the ignition coil within 50
cm (19.7 in) each other. Be careful not to get an electrical
shock while checking, because the electrical discharge
voltage becomes 20 kV or more.
- It might damage the ignition coil if the gap of more than 17 mm (0.66
in) is made.
NOTE:
When the gap is less than 13 mm (0.52 in), a spark might be generated even if
the coil is malfunctioning.
7.CHECK FUNCTION OF IGNITION COIL-II
- Turn ignition switch OFF.
- Disconnect spark plug and connect a non-malfunctioning spark plug.
- Crank engine for about 3 seconds, and recheck whether spark is
generated between the spark plug and
the grounded metal portion.
Spark should be generated
8.CHECK SPARK PLUG
Check the initial spark plug for fouling, etc.
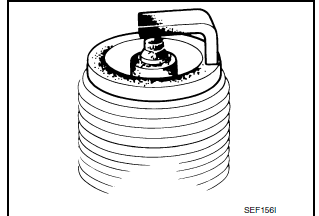
9.CHECK FUNCTION OF IGNITION COIL-III
- Reconnect the initial spark plugs.
- Crank engine for about three seconds, and recheck whether spark is
generated between the spark plug
and the grounded portion.
10.CHECK FUEL INJECTOR
- Turn ignition switch OFF.
- Remove fuel injector assembly.
Refer to EM-43, "Removal and Installation".
Keep fuel hose and all fuel injectors connected to fuel tube.
- Disconnect all ignition coil harness connectors.
- Reconnect all fuel injector harness connectors disconnected.
- Turn ignition switch ON.
Check that fuel does not drip from fuel injector.
11.CHECK INTERMITTENT INCIDENT
Description
The camshaft position sensor (PHASE) senses the retraction of
camshaft (INT) to identify a particular cylinder. The camshaft position
sensor (PHASE) senses the piston position.
...
DTC Logic
DTC DETECTION LOGIC
NOTE:
If DTC P0441 is displayed with other DTC such as P2122, P2123, P2127, P2128 or
P2138, first perform
trouble diagnosis for other DTC.
In this evaporative em ...
Other materials:
Using the panic alarm
If you are near your vehicle and feel threatened,
you may activate the panic alarm to call attention
by pressing and holding the button
on the
Intelligent Key for longer than 1 second.
The panic alarm and headlights will stay on for a
period of time.
The panic alarm stops when:
It ...
Meter
Wiring Diagram
...
Diagnosis and repair workflow
Work Flow
OVERALL SEQUENCE
DETAILED FLOW
1.CHECK SYMPTOM
Check the malfunction symptoms by performing the following items.
Interview the customer to obtain the malfunction information (conditions
and environment when the malfunction
occurred).
Check the symptom.
2.SELF-DIAGNOS ...