Nissan Maxima Service and Repair Manual: P0453 evap control system pressure sensor
Description
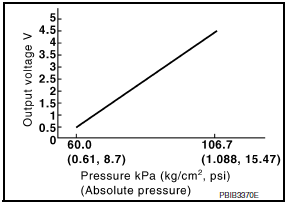
The EVAP control system pressure sensor detects pressure in the
purge line. The sensor output voltage to the ECM increases as pressure
increases.
DTC Logic
DTC DETECTION LOGIC
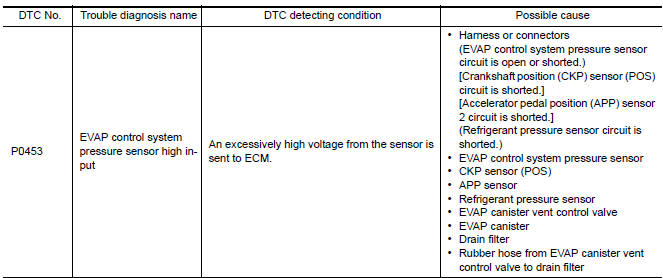
DTC CONFIRMATION PROCEDURE
1.PRECONDITIONING
If DTC Confirmation Procedure has been previously conducted, always perform
the following before conducting
the next test.
- Turn ignition switch OFF and wait at least 10 seconds.
- Turn ignition switch ON.
- Turn ignition switch OFF and wait at least 10 seconds.
TESTING CONDITION:
Always perform test at a temperature of 5C (41F) or more.
2.PERFORM DTC CONFIRMATION PROCEDURE
With CONSULT
- Start engine and warm it up to normal operating temperature.
- Turn ignition switch OFF and wait at least 10 seconds.
- Turn ignition switch ON.
- Turn ignition switch OFF and wait at least 10 seconds.
- Turn ignition switch ON.
- Select "DATA MONITOR" mode with CONSULT.
- Check that "FUEL T/TMP SE" is more than 0C (32F).
- Start engine and wait at least 20 seconds.
- Check 1st trip DTC.
With GST
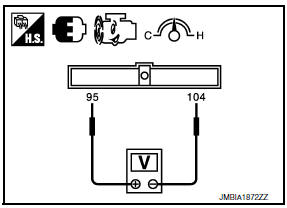
- Start engine and warm it up to normal operating temperature.
- Set voltmeter probes to ECM harness connector terminals.
- Check that the voltage is less than 4.2 V.
- Turn ignition switch OFF and wait at least 10 seconds.
- Turn ignition switch ON.
- Turn ignition switch OFF and wait at least 10 seconds.
- Start engine and wait at least 20 seconds.
- Check 1st trip DTC.
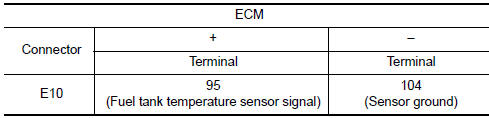
Diagnosis Procedure
1.CHECK GROUND CONNECTION
- Turn ignition switch OFF.
- Check ground connection E9.
2.CHECK CONNECTOR
- Disconnect EVAP control system pressure sensor harness connector.
- Check that water is not inside connectors.
3.CHECK EVAP CONTROL SYSTEM PRESSURE SENSOR POWER SUPPLY CIRCUIT
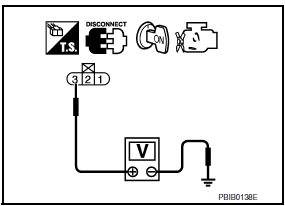
- Turn ignition switch ON.
- Check the voltage between EVAP control system pressure sensor
harness connector and ground.

4.CHECK EVAP CONTROL SYSTEM PRESSURE SENSOR POWER SUPPLY CIRCUIT-II
- Turn ignition switch OFF.
- Disconnect ECM harness connector.
- Check the continuity between EVAP control system pressure sensor
harness connector and ECM harness
connector.

5.DETECT MALFUNCTIONING PART
Check the following.
- Harness connectors B10, E29
- Harness for open or short between EVAP control system pressure
sensor and ECM
6.CHECK SENSOR POWER SUPPLY CIRCUIT
Check harness for short to power and short to ground, between the following
terminals.
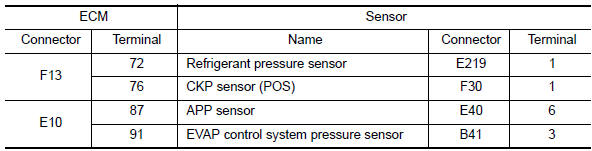
7.CHECK COMPONENTS
Check the following.
- Crankshaft position sensor (POS) (Refer to EC-299, "Component
Inspection".)
- Refrigerant pressure sensor
8.CHECK APP SENSOR
9.REPLACE ACCELERATOR PEDAL ASSEMBLY
- Replace accelerator pedal assembly
10.CHECK EVAP CONTROL SYSTEM PRESSURE SENSOR GROUND CIRCUIT FOR OPEN AND
SHORT
- Turn ignition switch OFF
- Disconnect ECM harness connector.
- Check the continuity between EVAP control system pressure sensor
harness connector and ECM harness
connector.
- Also check harness for short to ground and short to power.

11.DETECT MALFUNCTIONING PART
Check the following.
- Harness connectors B10, E29
- Harness for open or short between EVAP control system pressure
sensor and ECM
12.CHECK EVAP CONTROL SYSTEM PRESSURE SENSOR INPUT SIGNAL CIRCUIT FOR OPEN
AND SHORT
- Check the continuity between EVAP control system pressure sensor
harness connector and ECM harness
connector.
- Also check harness for short to ground and short to power.

13.DETECT MALFUNCTIONING PART
Check the following.
- Harness connectors B10, E29
- Harness for open or short between EVAP control system pressure
sensor and ECM
14.CHECK RUBBER TUBE
- Disconnect rubber tube connected to EVAP canister vent control
valve.
- Check the rubber tube for clogging.
15.CHECK EVAP CANISTER VENT CONTROL VALVE
16.CHECK EVAP CONTROL SYSTEM PRESSURE SENSOR
17.CHECK DRAIN FILTER
18.CHECK IF EVAP CANISTER IS SATURATED WITH WATER
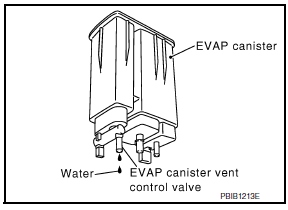
- Remove EVAP canister with EVAP canister vent control valve and
EVAP control system pressure sensor
attached. Refer to FL-14, "Removal and Installation (EVAP Canister)".
- Check if water will drain from the EVAP canister
19.CHECK EVAP CANISTER
Weigh the EVAP canister with the EVAP canister vent control valve and EVAP
control system pressure sensor
attached.
The weight should be less than 2.1 kg (4.6 lb).
20.DETECT MALFUNCTIONING PART
Check the following.
- EVAP canister for damage
- EVAP hose between EVAP canister and drain filter for clogging or
poor connection
21.CHECK INTERMITTENT INCIDENT
Component Inspection
EVAP CONTROL SYSTEM PRESSURE SENSOR
1.CHECK EVAP CONTROL SYSTEM PRESSURE SENSOR
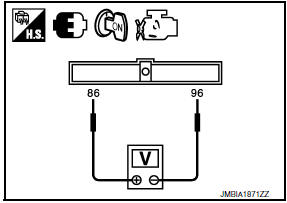
- Turn ignition switch OFF.
- Remove EVAP control system pressure sensor with its harness
connector. Refer to FL-17, "Removal and
Installation".
Always replace O-ring with a new one.
- Install a vacuum pump to EVAP control system pressure sensor.
- Turn ignition switch ON and check output voltage between ECM
terminals under the following conditions.
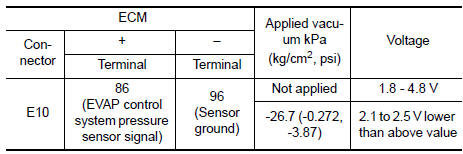
CAUTION:
- Always calibrate the vacuum pump gauge when using it.
- Never apply below -93.3 kPa (-0.952 kg/cm2, -13.53 psi) or
pressure over 101.3 kPa (1.033 kg/cm2,
14.69 psi).
DRAIN FILTER
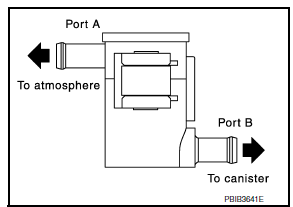
- Check visually for insect nests in the drain filter air inlet.
- Check visually for cracks or flaws in the appearance.
- Check visually for cracks or flaws in the hose.
- Blow air into port A and check that it flows freely out of port B.
- Block port B.
6. Blow air into port A and check that there is no leakage.
7. If NG, replace drain filter.
Description
The EVAP control system pressure sensor detects pressure in the
purge line. The sensor output voltage to the ECM increases as pressure
increases.
DTC Logic
DTC DETECTION LOGIC
...
DTC Logic
DTC DETECTION LOGIC
This diagnosis detects a very large leakage (fuel filler cap fell off etc.)
in EVAP system between the fuel tank
and EVAP canister purge volume control solenoid val ...
Other materials:
Seat memory indicator lamp
Description
Memory switch is equipped on the seat memory switch installed to the
driver side door trim. The operation signal is input to the driver seat
control unit when the memory switch is operated.
The status of automatic drive positioner system can be checked according
to the ill ...
Precaution
Precaution for Supplemental Restraint System (SRS) "AIR BAG" and
"SEAT BELT PRE-TENSIONER"
The Supplemental Restraint System such as "AIR BAG" and "SEAT BELT
PRE-TENSIONER", used along with a front seat belt, helps to reduce the risk
or severity of injury to the driver and front passenger for ...
System temporarily unavailable
The following are conditions in which the ICC
system may be temporarily unavailable. In these
instances, the ICC system may not cancel and
may not be able to maintain the selected following
distance from the vehicle ahead.
Condition A
Under the following conditions, the ICC system is
auto ...