Nissan Maxima Service and Repair Manual: Front drive shaft
Removal and Installation (LH)
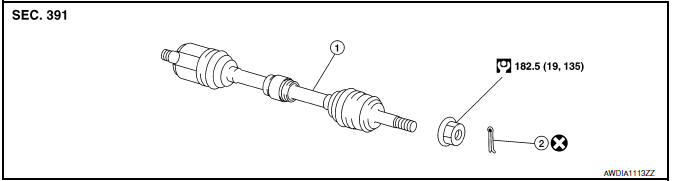
- Drive shaft
- Cotter pin
REMOVAL
- Remove wheel and tire using power tool. Refer to WT-60, "Adjustment".
- Remove wheel sensor from steering knuckle. Refer to BRC-102,
"Removal and Installation - Front Wheel Sensor".
CAUTION: Do not
pull on wheel sensor harness.
- Remove brake hose lock plate from strut assembly.
- Remove brake caliper torque member bolts using power tool leaving
brake hose attached, then remove disc rotor. Reposition caliper aside
with wire. Refer to BR-32, "Removal and Installation of Brake Caliper and
Rotor".
NOTE: Avoid depressing brake pedal while brake caliper is
removed.
- Remove cotter pin, then loosen lock nut from drive shaft using
power tool.
- . Remove lower strut bolts and nuts using power tool. Refer to FSU-13,
"Exploded View".
- Using a piece of wood and a hammer, tap on lock nut to disengage
drive shaft from wheel hub.
CAUTION:
- Do not place drive shaft joint at an extreme angle. Also be
careful not to overextend slide joint.
- Do not allow drive shaft to hang down without support.
NOTE: Use suitable puller if drive shaft
cannot be separated from wheel hub and bearing assembly.
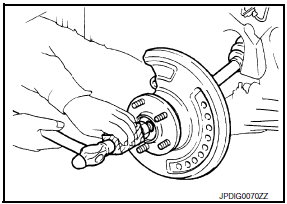
- Remove drive shaft from transaxle assembly.
- Use Tool (A) and sliding hammer (B) while inserting tip of tool
between housing and transaxle assembly.
CAUTION: Do not place drive shaft joint at
an extreme angle when removing drive shaft. Also be careful not to overextend
slide joint.
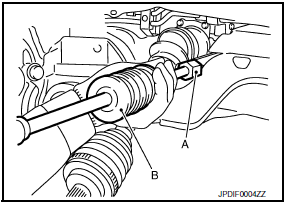
Tool number (A) : KV40107500 ( - )
INSPECTION AFTER REMO
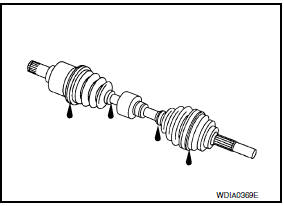
- Move joint up/down, left/right, and in axial direction. Check for any
rough movement or significant looseness.
- Check boot for cracks or other damage, and for grease leakage.
- If damaged, disassemble drive shaft to verify damage, and repair or
replace as necessary.
INSTALLATION
Installation is in the reverse order of removal. Note the following:
CAUTION: Do not reuse cotter pin.
- Install new circlip on drive shaft in the circular clip groove on
transaxle side. Refer to FAX-13, "Disassembly and Assembly (LH)".
CAUTION: Make sure the new circlip on
the drive shaft is securely fastened.
- In order to prevent damage to differential side oil seal, place
Tool (A) onto oil seal before inserting drive shaft as shown. Slide drive
shaft into slide joint and tap with a hammer to install securely.
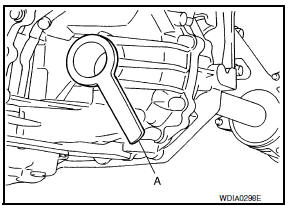
Tool number (A) : KV38107900 ( - )
CAUTION: Make sure that circlip is completely
engaged.
INSPECTION AFTER INSTALLATION
- Check wheel alignment. Refer to FSU-6, "Inspection and
Adjustment".
- Adjust neutral position of steering angle sensor. Refer to BRC-6,
"ADJUSTMENT OF STEERING ANGLE SENSOR NEUTRAL POSITION : Special Repair
Requirement".
Removal and Installation (RH)
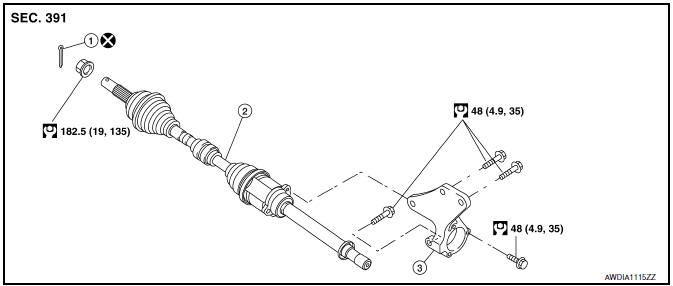
- Cotter pin
- Drive shaft
- Support bearing bracket
REMOVAL
- Remove wheel and tire using power tool. Refer to WT-60, "Adjustment".
- Remove wheel sensor from steering knuckle. Refer to BRC-102,
"Removal and Installation - Front Wheel Sensor".
CAUTION: Do not pull on wheel sensor harness.
- Remove brake hose lock plate from strut assembly.
- Remove brake caliper torque member bolts using power tool leaving
brake hose attached, then remove disc rotor. Reposition caliper aside
with wire. Refer to BR-32, "Removal and Installation of Brake Caliper and
Rotor".
NOTE: Avoid depressing
brake pedal while brake caliper is removed.
- Remove cotter pin, then loosen lock nut from drive shaft using
power tool.
- Remove lower strut bolts and nuts using power tool. Refer to
FSU-13, "Exploded View".
- Using a piece of wood and a hammer, tap on lock nut to disengage
drive shaft from wheel hub.
CAUTION:
- Do not place drive shaft joint at an extreme angle. Also be
careful not to overextend slide joint.
- Do not allow drive shaft to hang down without support.
NOTE: Use suitable puller if drive shaft
cannot be separated from wheel hub and bearing assembly.
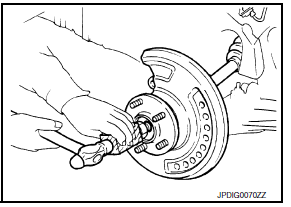
- Remove bearing housing to support bearing bracket bolts.
- Remove drive shaft from transaxle assembly.
- Use Tool (A) and sliding hammer (B) while inserting tip of tool
between housing and transaxle assembly.
CAUTION: Do not place drive shaft joint at
an extreme angle when removing drive shaft. Also be careful not to overextend
slide joint.
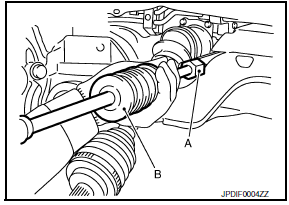
Tool number (A) : KV40107500 ( - )
- If necessary, remove the support bearing bracket.
- Remove front exhaust tube. Refer to EX-5, "Removal and
Installation".
INSPECTION AFTER REMOVAL
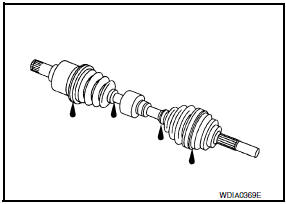
- Move joint up/down, left/right, and in axial direction. Check for
any rough movement or significant looseness.
- Check boot for cracks or other damage, and for grease leakage.
- If damaged, disassemble drive shaft to verify damage, and repair
or replace as necessary
INSTALLATION
Installation is in the reverse order of removal. Note the following:
CAUTION: Do not reuse cotter pin.
- Install new circlip on drive shaft in the circular clip groove on
transaxle side. Refer to FAX-19, "Disassembly and Assembly (RH)".
CAUTION: Make sure the new circlip on the
drive shaft is securely fastened.
- In order to prevent damage to differential side oil seal, place
Tool (A) onto oil seal before inserting drive shaft as shown. Slide drive
shaft into slide joint and tap with a hammer to install securely.
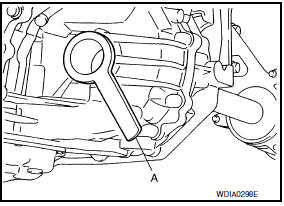
Tool number (A) : KV38107900 ( - )
CAUTION: Make sure that circlip is completely
engaged.
- When installing support bearing bracket, hand tighten the bolts, then
tighten to specified torque.
INSPECTION AFTER INSTALLATION
- Check wheel alignment. Refer to FSU-6, "Inspection and
Adjustment".
- Adjust neutral position of steering angle sensor. Refer to BRC-6,
"ADJUSTMENT OF STEERING ANGLE SENSOR NEUTRAL POSITION : Special Repair
Requirement".
Removal and Installation
Steering knuckle
Splash guard
Wheel hub and bearing assembly
Cotter pin
REMOVAL
Remove wheel and tire using power tool. Refer to ...
FRONT DRIVE SHAFT
Disassembly and Assembly (LH)
Circlip
Dust shield
Housing
Snap ring
Spider assembly
Stopper ring
Boot band
Boot
Shaft
D ...
Other materials:
Brake booster
Exploded View
Master cylinder assembly
Brake booster
Brake pedal
Lock nut
Gasket
Removal and installation
NOTE:
When removing components such as hoses, tubes/lines, etc., cap or plug openings
to prevent fluid from spilling.
REMOVAL
Release the fuel pressure. Refer to ...
B260A ignition relay
Description
BCM turns ON the following relays to ignition power supply to each ECU when
the ignition switch is turned
ON.
Ignition relay-1 (inside IPDM E/R)
Ignition relay-2 (inside fuse block (J/B))
Front blower motor relay
BCM checks any ignition relay ON request for consistency wi ...
Fuel recommendation
NISSAN recommends the use of unleaded premium
gasoline with an octane rating of at least
91 AKI (Anti-Knock Index) number (Research
octane number 96). If unleaded premium gasoline
is not available, you may use unleaded regular
gasoline with an octane rating of at least 87 AKI
number (Research ...