Nissan Maxima Service and Repair Manual: Cooling fan control
System Diagram
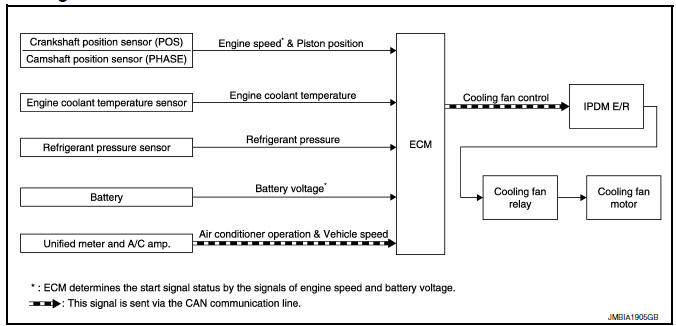
System Description
INPUT/OUTPUT SIGNAL CHART
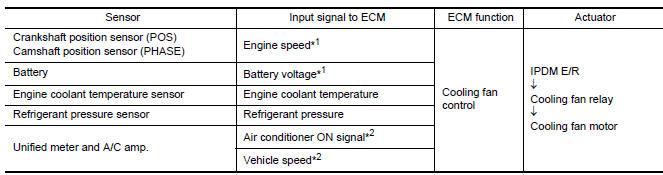
*1: The ECM determines the start signal status by the signals of engine speed
and battery voltage.
*2: This signal is sent to ECM via the CAN communication line.
SYSTEM DESCRIPTION
The ECM controls the cooling fan corresponding to the vehicle speed, engine
coolant temperature, refrigerant
pressure, and air conditioner ON signal. The control system has 4-step control
[HIGH/MIDDLE/LOW/OFF].
Cooling Fan Operation
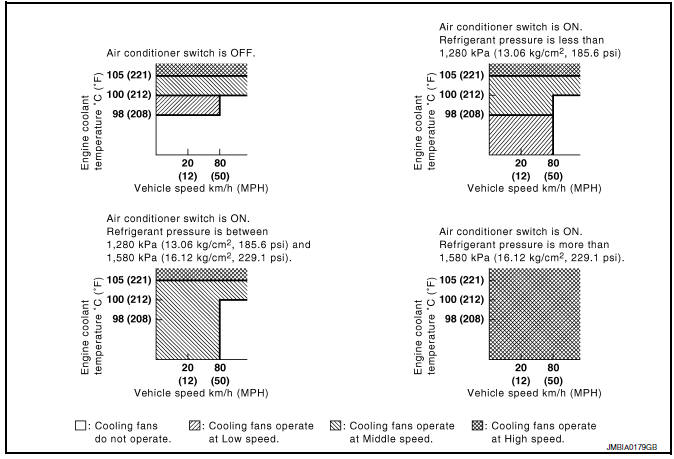
Cooling Fan Relay Operation
The ECM controls cooling fan relays in the IPDM E/R via the CAN communication
line.

Component Parts Location
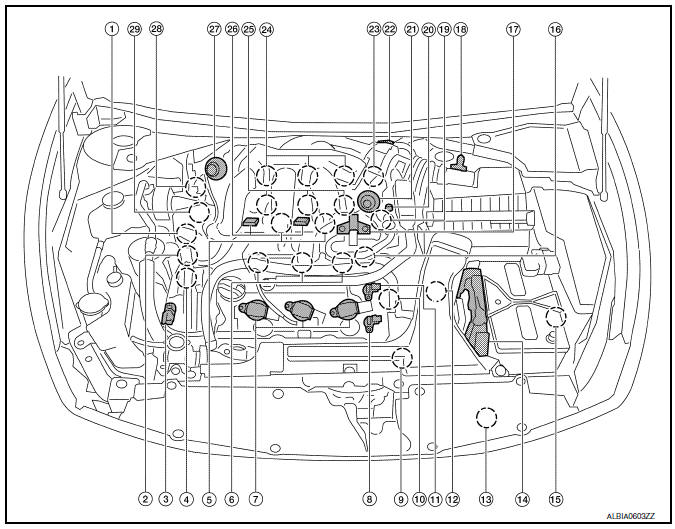
- Intake valve timing control solenoid
valve (bank 1)
- Electronic controlled engine mount
control solenoid valve
- Exhaust valve timing control magnet
retarder (bank 2)
- Intake valve timing control solenoid
valve (bank 2)
- Knock sensor (bank 1 and 2)
- Fuel injector (bank 2)
- Ignition coil (with power transistor) and
spark plug (bank 2)
- Exhaust valve timing control position
sensor (bank 2)
- Crankshaft position sensor (POS)
- Engine coolant temperature sensor
- Camshaft position sensor (PHASE)
(bank 2)
- Transmission range switch
- Refrigerant pressure sensor
- ECM
- Battery current sensor
- Condenser-2
- EVAP canister purge volume control
solenoid valve
- Mass air flow sensor (with intake air
temperature sensor)
- Camshaft position sensor (PHASE)
(bank 1)
- EVAP service port
- Power valve actuator 2
- Electric throttle control actuator
- Exhaust valve timing control position
sensor (bank 1)
- Ignition coil (with power transistor) and
spark plug (bank 1)
- Fuel injector (bank 1)
- VIAS control solenoid valve 1 and 2
- Power valve actuator 1
- Exhaust valve timing control magnet
retarder (bank 1)
- Power steering pressure sensor
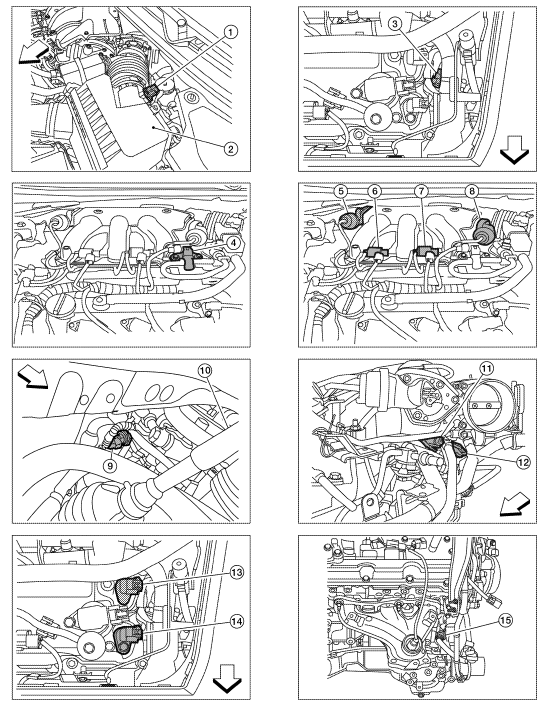
- Mas air flow sensor (with intake air
temperature sensor)
- Air cleaner case
- Engine coolant temperature sensor
(view with engine cover removed)
- EVAP canister purge volume control
solenoid valve (view with engine cover
removed)
- Power valve actuator 1 (view with engine
cover removed)
- VIAS control solenoid valve 1
- VIAS control solenoid valve 2
- Power valve actuator 2
- Power steering pressure sensor
- Tie rod (RH)
- Camshaft position sensor (PHASE)
(bank 1) (view with air cleaner case removed)
- Exhaust valve timing control position
sensor (bank 1)
- Camshaft position sensor (PHASE)
(bank 2) (view with air cleaner case removed)
- Exhaust valve timing control position
sensor (bank 2)
- Engine oil temperature sensor
: Vehicle front
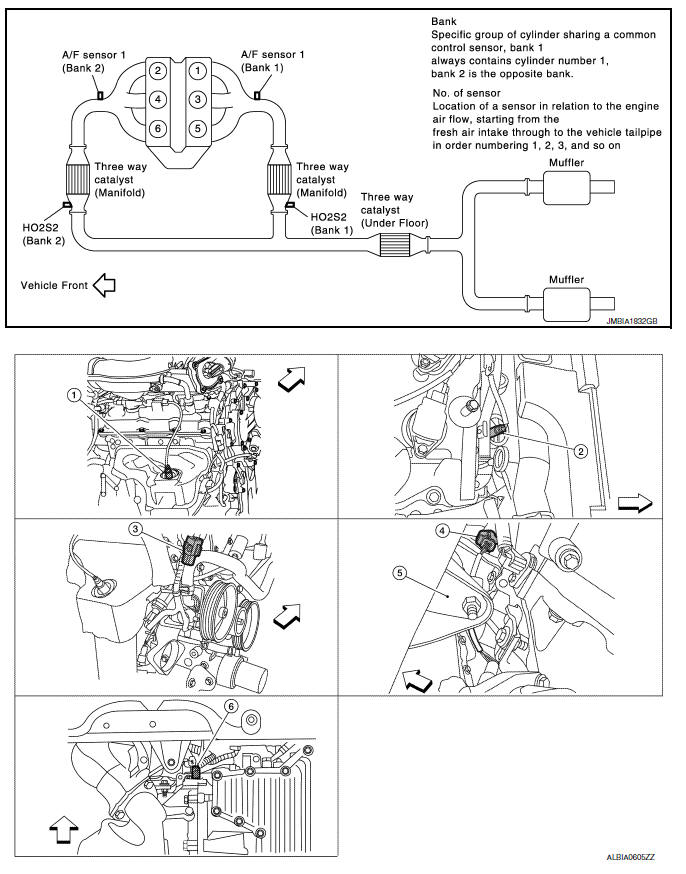
- A/F sensor 1 (bank 1) (view with engine
removed)
- A/F sensor 1 (bank 2)
- HO2S2 (bank 1) harness connector
(view with engine removed)
- HO2S2 (bank 2) harness connector
- Front engine mount
- Crankshaft position sensor (POS)
: Vehicle front
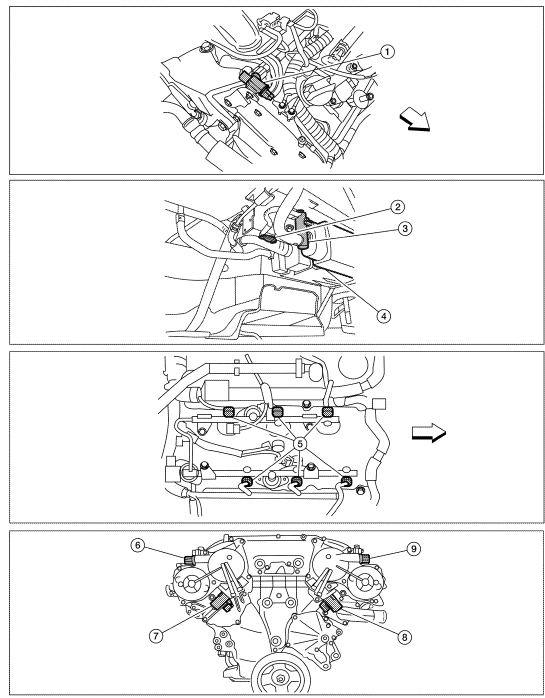
- Electronic controlled engine mount
control solenoid valve (view with engine
cover removed)
- EVAP control system pressure sensor
(view with rear suspension member removed)
- EVAP canister vent control valve
- EVAP canister
- Fuel injector harness connector (view
with intake manifold collector removed)
- Exhaust valve timing control magnet
retarder (bank 1) (view with engine removed)
- Intake valve timing control solenoid
valve (bank 1)
- Intake valve timing control solenoid
valve (bank 2)
- Exhaust valve timing control magnet
retarder (bank 2)
: Vehicle front
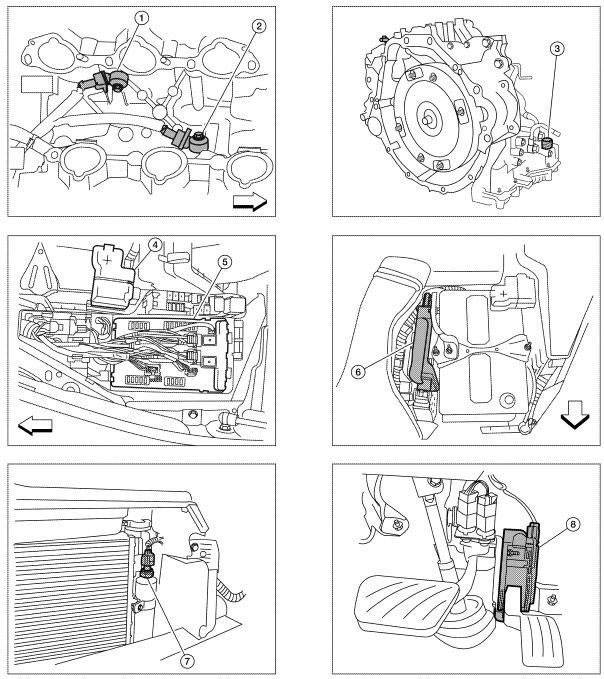
- Knock sensor (bank 2) (view with intake
manifold removed)
- Knock sensor (bank 1)
- Transmission range switch
(view with CVT removed)
- Battery
- IPDM E/R
- ECM
- Refrigerant pressure sensor (view
with front grille removed)
- Accelerator pedal position sensor
: Vehicle front
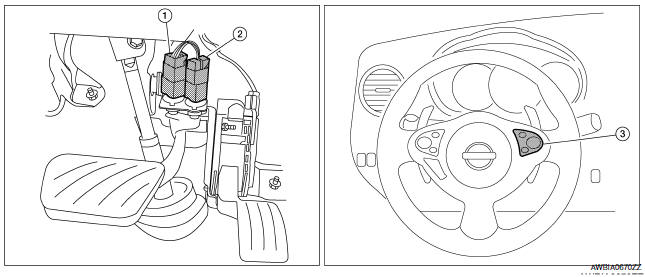
- Stop lamp switch
- ASCD brake switch
- ASCD steering switch
Component Description
Component Reference
- Camshaft position sensor (PHASE) EC-300, "Description"
- Crankshaft position sensor (POS) EC-296, "Description"
- Cooling fan motor EC-486, "Description"
- Engine coolant temperature sensor EC-201, "Description"
- Refrigerant pressure sensor
System Description
CAN (Controller Area Network) is a serial communication line for real time
application. It is an on-vehicle multiplex
communication line with high data communication speed and ...
System Diagram
System Description
INPUT/OUTPUT SIGNAL CHART
*: This signal is sent to the ECM via the CAN communication line.
SYSTEM DESCRIPTION
The ECM controls the engine mount operatio ...
Other materials:
Front tweeter
Removal and Installation
REMOVAL
Remove the front pillar finisher. Refer to INT-24, "Removal and
Installation".
Remove the front tweeter speaker grille. Refer to IP-10, "Exploded
View".
Remove the front tweeter speaker screws (A).
Pull out front tweeter speaker ( ...
Rear seat
Exploded View - Fixed Seatback
Headrest
Headrest holder (free)
Headrest holder (locked)
Bumper
Seatback assembly
Seatback trim
Seatback pad
Seat cushion trim
Seat cushion pad
Seat cushion wire cover
Seat cushion lock
Seat cushion assembly
Removal and Installati ...
Unit removal and installation
Rear suspension assembly
Exploded View
Rear shock absorber cap
Strut mount insulator
Shock absorber mount seal
Rear suspension bound bumper
Rear shock absorber
Rear suspension arm
Connecting rod mount bracket
Rear stabilizer connecting rod
Rear spring upper rubber seat ...